Your basket is currently empty!
Battersea Power Station – Phase 2 involved the restoration and redevelopment of the iconic Grade II listed building. The project included the creation of commercial, retail, residential, and leisure spaces within the historic structure.
BACKGROUND TO THE PROJECT
The Battersea Power Station redevelopment is one of the UK’s most ambitious regeneration projects, transforming a decommissioned power station into a vibrant mixed-use community. This phase focused on the careful refurbishment of the landmark building, maintaining its historic architectural elements while integrating modern facilities.
Protec has a longstanding relationship with Mace, having worked together on various large-scale projects, providing high-quality temporary protection solutions that align with their sustainability objectives.
THE CHALLENGE
The redevelopment of an iconic and historic structure posed unique challenges. Temporary protection was required across multiple applications to safeguard glazing, floors, doors, and joinery from damage during construction.
The site was high traffic with intensive contractor activity, necessitating robust and sustainable protection materials. Additionally, Mace was committed to reducing waste and minimising environmental impact, requiring an innovative and effective recycling solution.
PROJECT SOLUTION
Protec collaborated with Mace and its subcontractors from the outset to implement the Proplex ClosedLoop Remanufacturing Scheme. This initiative ensured that the temporary protection used on-site could be recovered, recycled, and remanufactured into new ProplexRE sheets for future projects. Protec provided expert guidance on protection strategies and worked closely with Mace’s site logistics team Clipfine and waste-away partner MSK to facilitate smooth recovery operations.
Our involvement in this high-profile project was significant, with large volumes of Proplex sheets supplied and later recovered for recycling at our state-of-the-art UK manufacturing and recycling facility.
THE OUTCOME
The project was successfully completed with effective protection measures in place. Protec’s sustainable ClosedLoop Remanufacturing Scheme delivered tangible environmental benefits. The remanufactured ProplexRE sheets have already been redeployed on other construction projects, demonstrating the practical benefits of a circular economy approach.
Protec continues to collaborate with Mace and its subcontractors on other projects, helping them achieve their sustainability targets through innovative and environmentally responsible temporary protection solutions.
“It has been great to work with Protec on their ClosedLoop remanufacturing scheme for plastic protective sheeting. This has helped Mace’s commitment to reducing waste on our construction projects by allowing this material to be remanufactured in large quantities at Protec’s facility. Keeping the remanufacture in the UK also lowers the carbon impact and overall reduces the need for virgin raw material extraction and the carbon emissions involved in the manufacturing process.”
Lynne Burden – Senior Sustainability Manager, Mace
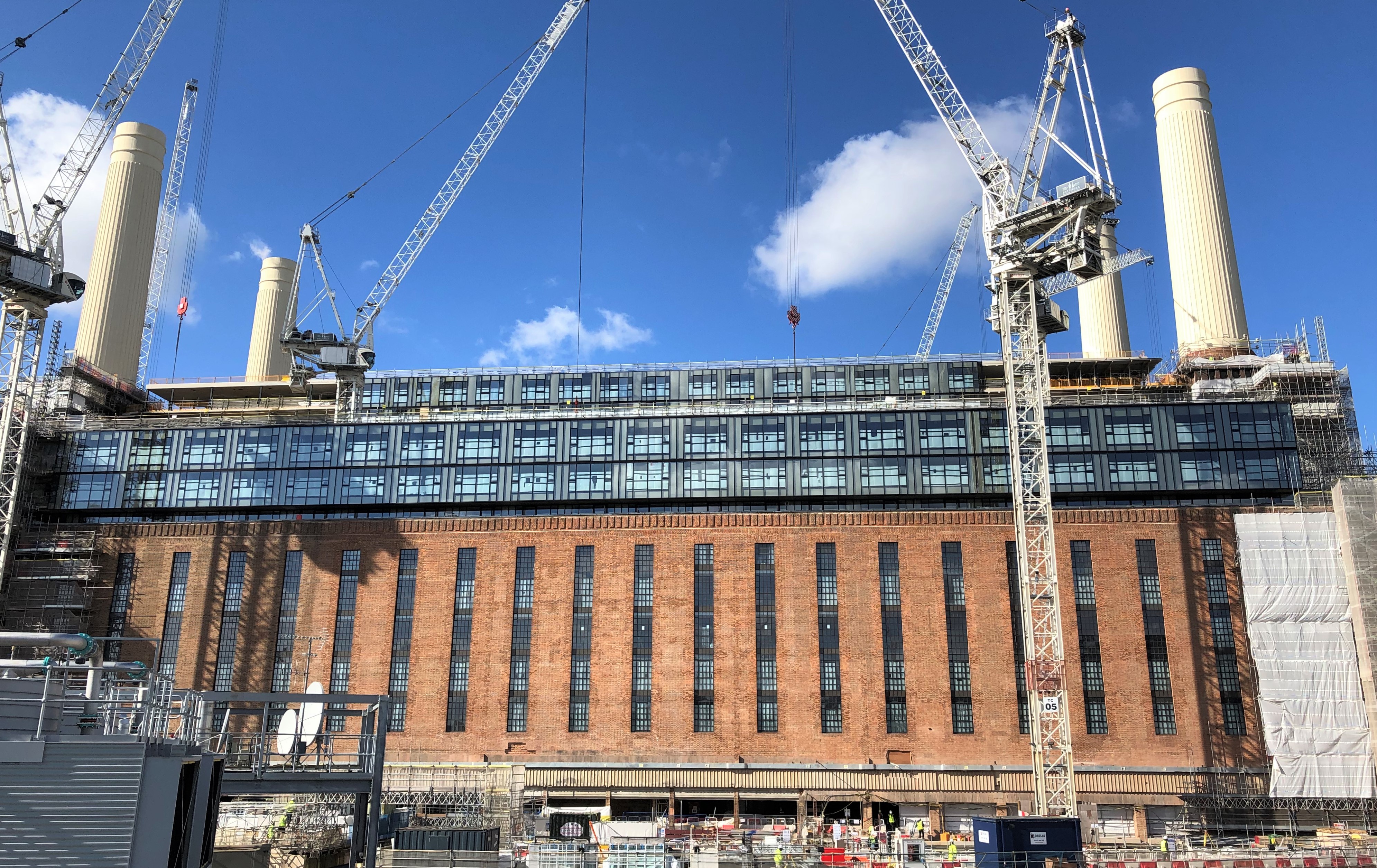
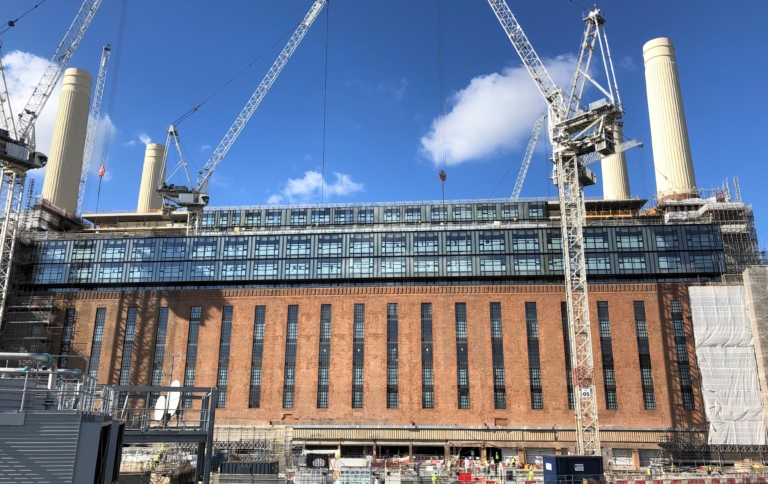
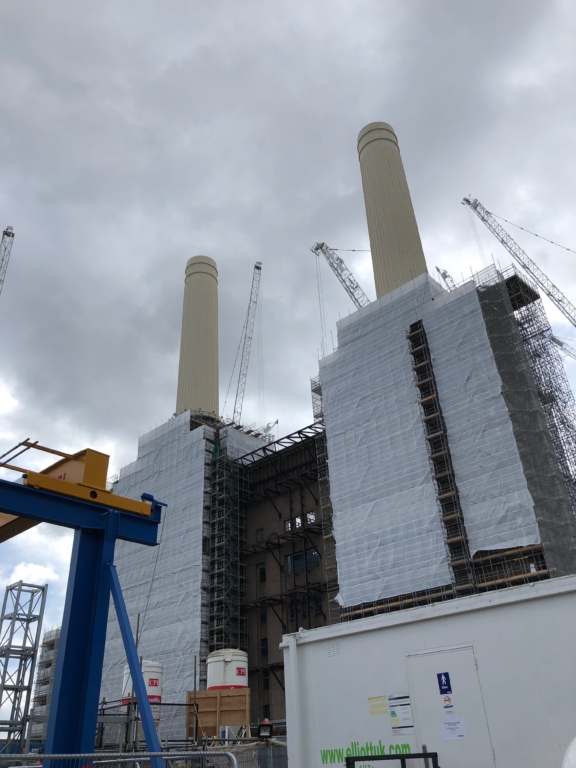
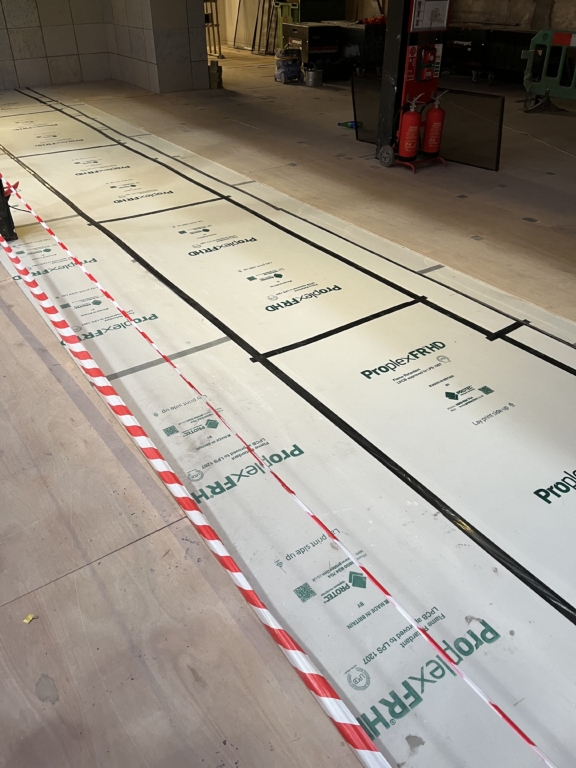
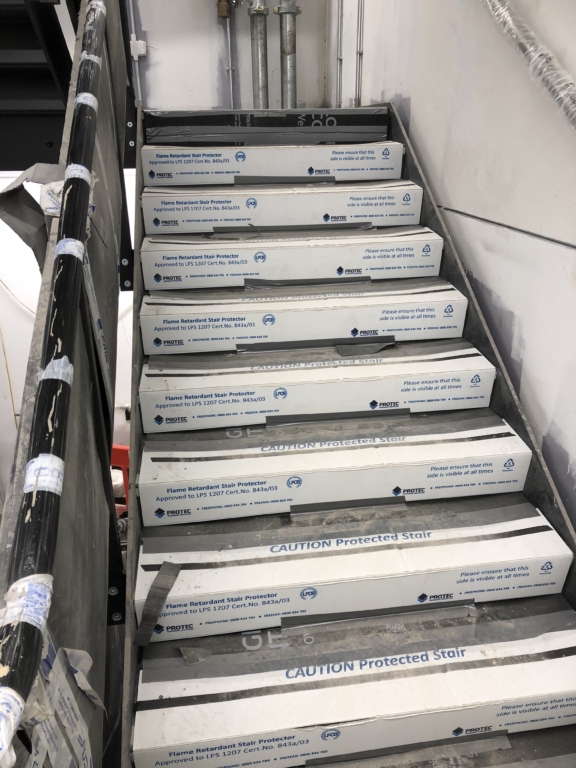
Share